Tile Factory Tour Shows How Cement Tiles are Made
Posted by William Buyok on
Once question I get a lot is, "How are cement tiles made?" It's a great question because cement tiles or encaustic cement tiles are very different from ceramic and porcelain tiles. Unlike glazed ceramics tiles, these tiles aren't painted, or glazed or fired in a kiln. The pattern found in cement tiles is created by pouring pigmented concrete into a mold. This unique process dates to the mid-19th century. Cement tiles should really be called concrete tiles because cement is an ingredient that is used to make concrete; but, there's no going back now.
A colorful floor pattern created with handmade cement tiles
In today's post, I provide a detailed explanation of the step-by-step process of making these unique tiles. The explanations are more detailed than, How Encaustic Cement Tiles are Made, in our Cement Tile Info Center. These photos are from a factory I visited a several years ago. While visiting the factory, I met the owners and got to see the expert tile makers at their craft.
Special thanks to the kindness and warmth of the factory owners for allowing me to share both the inner workings of a cement tile factory and bringing well-deserved attention to the hands that touch each and every tile they make. I hope you enjoy this factory tour and walk away with a better appreciation and understanding of why handmade cement tile is truly a labor of love.
Mixing the Color Layer of Cement Tile
Calcium carbonate in these bins will be mixed to form the color layer
The color layer of handmade cement tiles is about 1/8" thick. The color layer is the tile's face and the part of the tile you walk on and see when installed. The color layer is made from a mixture of the following:- White Portland cement
- Marble dust
- Silica sand
- Calcium carbonate
- Mineral pigments (such as iron, cobalt and chromium oxides)
The color layer is prepared in batches and every component is weighed in order to achieve color consistency. The color is mixed in a horizontal mixer that guarantees the homogenization of the mixture. The large ball, shown below, is used to help achieve these manufacturing requirements.
The color layer materials are mixed in the horizontal mixer
For small batches, strike-offs, and samples, only a small amount of color is mixed in a bucket and blended with a "hand mixer."
Cement Tile Molds Create the Tile's Pattern
Patterned tiles are created using a mold that follows the lines of the pattern. Molds are made from steel in a machine shop. At least one mold for each piece of the pattern is needed. A crisp outline in the pattern is only achieved by maintaining tightly machined tolerances between the pattern mold and the steel plate the mold sits on. Molds are checked against full size drawings and tested until the pattern is correct and the lines crisp.
Here's the cement tile mold library where molds are housed for existing patterns. If you want a new pattern or pattern in a different size, then a custom mold will need to be created. The pattern mold sits inside the frame or format mold. The frame determines and molds the tile shape (i.e., 8" x 8" or hexagon). The pattern mold determines the design on the tile's face.
Pigmented concrete is poured into a pattern mold like this
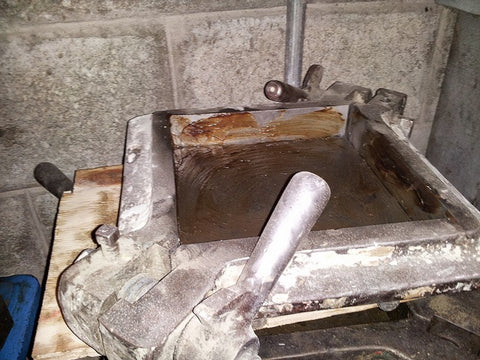
Hand Making Cement Tile
Each station is manned and operated by an expert cement tile maker and a mi ayudante, or my helper, in Spanish. The helper allows the expert tile maker to focus on getting the right colors in the mold slots, keeps the liquid cement tile bins full, and makes sure there is plenty of sand for the second and third layer. Without a helper, the time to make a tile would more than double.
The color is then mixed with water in mixing bins located at each station.
The colored cement is hand-poured into the different sections of the molds. The thickness of the color layer will always be between 3 to 5 millimeters (about 1/8"). Then, the pattern mold is removed.
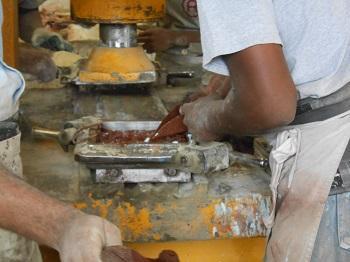
Two layers of cement and sand are poured on top of the color layer. These layers add strength and absorb water from the color layer.
Finally, the cement tile is pressed using a hydraulic press, which applies 1,700 PSI of pressure. The tiles are then placed on racks as they come off the line.
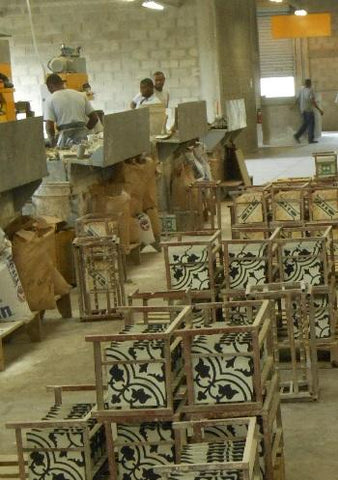
The following day, the cement tiles are soaked in water in order to achieve water saturation and hardness. The water bath guarantees proper cement hydration.
The tiles are left to dry for 10 days and then hand-inspected. After 28 days from start of manufacturing, the cement tile color surface will have obtained 98% of its hardness and is usually ready to be installed.
Watch Cement Tiles Being Made
These short videos were filmed at the factory and show pattern, plain, and hexagon cement tiles being made.
Making Patterned Cement Tile
The pigmented cement is hand-poured into the patterned mold. The mold is removed. Two additional layers of cement are added for strength and water absorption. The bolted frame holds the cement in place until it is hydraulically pressed. Removing the frame exposes the tile!
Making Plain or Solid Color Cement Tile
Watch solid-color cement tiles being made. The pigmented cement is hand-poured into the mold. Additional layers of cement are added for strength and water absorption. The cement tile is hydraulically pressed. Removing the frame, the tile is turned out.
Making Hexagonal Cement Tiles
Watch hexagonal cement tiles being made. Pigmented cement is hand-poured into a patterned mold. The mold is removed and additional layers of cement are added for strength and water absorption before the tile is hydraulically pressed. See the hexagon-shaped tile turned out.
Learn More About Cement Tiles
I hope you enjoyed the cement tile factory tour and have a better understanding of how cement tiles are made. You can see that making these tiles is a labor of love. The handcrafted nature of these tiles explains why there is variation in the tile shape and color. You can understand why lead times for custom orders can be two or three months. Now that you have an appreciation for the process, let us know what cement tile pattern and colors you'll be using for your next project. We've made it easy for you. Just stop by our Cement Tile Information Center to find the right cement tile for you.